Protecting Workers from Lead Exposure: An Awareness Guide for Construction Teams
Written by Staff Writer | Edited by Michael Purser
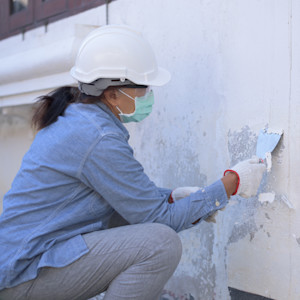
Many hazards in general industry and building settings may not be obvious — such as the risk from exposure to the toxic heavy metal known as lead.
Although the EPA mandated removal of this substance in the 1970s, many pre-1978 structures still contain materials like paint and pipes laced with it. As these materials deteriorate, they release dust that can contaminate indoor spaces. Individuals may inhale, ingest or absorb minute amounts, potentially resulting in severe complications — or even death.
Regulatory agencies require at-risk employees to complete annual instruction to mitigate contact with the metal. Let’s examine the basics of material absorption and its adverse effects, and explore how online instruction can help identify and reduce the risks.
What Are Contact Risks and OSHA Compliance Rules?
No one expects to encounter a dangerous heavy metal in their community or at work. Unfortunately, remnants of historical lead use can lurk in surprising places.
Some industries, such as construction, mining and manufacturing, require preventative safety protocols and compliance training to protect workers because of an elevated risk of encountering heavy metals in the air and on the skin during work.
How Does Contact Happen?
Employees may be at risk of encountering dangerous heavy metals while carrying out various tasks. Demolition, sanding, scraping, welding, heat gun use, abrasive blasting, and torch cutting all generate dust and fumes that may carry metal particles. Materials containing the metal can remain hidden until disturbances release dormant or fresh particles.
Employees may come into contact with the metal in three main ways:
Inhalation: The metal disintegrates into invisible, odorless dust during activities like demolition or welding, making detection difficult without testing.
Ingestion: Dust settling on surfaces can be swallowed by accident, with the metal only sometimes detectable by taste.
Skin Contact: Fine particles cling to surfaces and may transfer to the skin even after protective measures.
The Dangers of Lead Exposure
Exposure puts individuals at risk for multiple health risks, especially as lead bioaccumulates through repeated contact. Lead sticks around in the human body. Regulators are so strict about protective measures because the damage becomes worse over time.
Secondary hazards can affect people who were not directly exposed (like friends and family members) when workers unknowingly bring contaminated materials home.
Some of the negative health effects of lead exposure can include:
- High blood pressure
- Cardiovascular issues
- Kidney damage
- Reduced fetal growth and preterm birth in pregnant women
- Brain development issues in children
Federal Guidelines
OSHA’s lead standard in 29 CFR 1910.1025 states: “The employer shall train each employee who is subject to exposure to lead at or above the action level, or for whom the possibility of skin or eye irritation exists... The employer shall institute a training program and ensure employee participation in the program."
Regulators require employers to provide safety education for workers who are exposed to 30 micrograms of airborne particles per cubic meter of air averaged over eight hours.
Employers should address this particular danger in several ways. Beyond hazard communication— which requires employers to notify workers of potential risks — guidelines also advise employers to take the following steps, which are in order from the most effective to the least effective:
- Elimination: Physically remove the hazardous material from the workplace.
- Substitution: Replace lead-based products with a less toxic material.
- Engineering controls: Enclose the materials, isolate people from the hazard and/or install local exhaust ventilation.
- Administrative controls: Change the way people work around the material to minimize contact.
- Personal Protective Equipment (PPE): Protect workers with suitable PPE when working with or near leaded materials, especially respiratory protection.
As a worker, your primary responsibility is keeping up with current safe work practices and education requirements. If you work around this heavy metal, regulators expect you to take a lead awareness course once a year. Your employer is responsible for providing suitable instruction.
What to Look Out for When Evaluating Exposure Risks
You can do a lot to protect yourself from inhaling dangerous heavy metal particles at work as long as you stay aware and alert. According to the National Institute for Occupational Safety and Health (NIOSH), three key priorities are:
- Reading and following the guidelines your employer provides on safe work practices.
- Practicing good hygiene, working in well-ventilated areas and using PPE.
- Undergoing a medical evaluation, including a blood test, if you are concerned about possible exposure.
These are just the first steps. NIOSH gives more details concerning some of these points, including:
Hygiene
Since workers are primarily exposed to lead through dust particles, you can pay attention to your hygiene to minimize contact with dust. Consider doing the following:
- Keep your workplace clean: Use wet cleaning methods or a vacuum with a HEPA filter to take care of dust accumulation. Avoid using compressed air or dry sweeping so you don’t kick up dust.
- Wash your hands: Wash your hands regularly after work sessions to remove dust so you don’t spread it to your face or mouth. Keep in mind that standard soap and water won’t completely remove lead-contaminated metal dust. Use specialized wipes to completely remove dust.
- Shower at work: If possible, shower at work and change clothes before getting in your car and going home.
- Keep work clothes separate: If you clean your work clothes, keep them stored in a plastic bag away from other clothes. Wash and dry them separately.
Ventilation
Always use local exhaust ventilation when it’s available. If possible, work outside or open windows to improve airflow.
PPE
Make sure to wear and clean your PPE as instructed. Just like with cleaning your hands, you will need to use specialized wipes to remove dust from any PPE you are supposed to clean. If items become heavily soiled, such as work gloves, discard them and replace them with new ones.
Blood Tests
You can ask your employer if they do routine blood tests and request one for yourself. If they don’t, you can get a test from your regular healthcare provider.
What Is Lead Awareness Training?
As mentioned earlier, OSHA regulations address toxic metal hazards in the workplace by setting key protection measures and permissible contact limits. Online instruction for general industry shows one how to work securely around this heavy metal.
This course helps you understand:
- The health hazards associated with exposure
- Safety standards that address these risks
- The policies and procedures employers need to implement to protect you
- Safe work practices that can reduce your risk
The course meets the standards set by regulators for your annual safety education requirements. If your job involves handling other hazardous materials, you may also need Hazardous Waste Operations and Emergency Response (HAZWOPER) training.
Why Choose Us?
At OSHA Education Center, we strive to make it as convenient as possible to get high-quality online safety education. We are the go-to resource for general industry and construction professionals who want convenient, accessible compliance training.
We understand that your time is valuable. That’s why we offer all our courses — covering more than 150 other topics — 100% online. Our online programs are structured so that you can get the education you need when and where you need it.
Sign up and get started today!